Page 4 of 33
Posted: Fri Feb 23, 2007 10:06 am
by Hunt4em
Jim,
Looking forward to seeing those pics! I hope to see true Marlin colors. Best of luck to you!
Thanks, John
Posted: Fri Feb 23, 2007 3:25 pm
by Jim D
John,
I hope to see true Marlin colors too!!! Should have something to post tomorrow night, and whatever the results are, I'll post them.
-jim
True Marlin Case Colors
Posted: Fri Feb 23, 2007 4:44 pm
by Don Anderson
If you would like to see an example of a Marlin Model 1893 that still maintains 100% of the original case colors on the receiver, lever, hammer, tangs, and butt plate, check the catalog that is just coming out from the James D. Julia auction on March 12th. I have put my 1893 .38-55, checkered, 26" Oct. barrel and full mag., which was shipped on August 24, 1900, in their auction. This was the rifle that I was awarded one of the NRA's silver medallions for one of the "10 Best Weapons Displayed" at the 2006 NRA National Show. It's a rare example of a 107 year old Marlin that still has 100% original case colors.
Don
Posted: Fri Feb 23, 2007 9:41 pm
by Jim D
Don,
I'd love to see it!! Do they have the auction catalog online?
I'll bet that will be a hard one to part with...
-jim
Posted: Fri Feb 23, 2007 10:28 pm
by Jim D
Don,
OH MY! I found it online in the Julia catalog. That is one beautiful rifle!!!
Well, you've set the bar pretty high! Thanks for sharing the info Don.
-jim
Posted: Fri Feb 23, 2007 10:35 pm
by oodmoff
Don,
Mixed feelings stir abound when I hear of you parting with that rifle, I sure enjoyed hearing about it a few times in conversation with you. I guess every collector and his guns must one day part ways. But alas I know you did you best to keep that specific part of marlin history around and open for others to see and that in its self was a great thing to do. I sure hope that whomever takes over ownership is as gracious.
Case Colored Model 1893
Posted: Sat Feb 24, 2007 12:07 am
by Don Anderson
Thanks guys for the kind comments. If anyone would like to see pictures of the rifle, go to google and type in James Julia auction. Click on to the auction site and this gun will be in the second session and the lot number is 1117. Put this number into the search box and it will bring up five close up pictures of the rifle.
You're right.....it is tough to see this one go. I have really loved it and feel fortunate to have owned it for some years. But, as you guys know, we're only caretakers of our collections, so appreciate them while you have them.
Don
Posted: Sat Feb 24, 2007 8:37 pm
by Jim D
SECOND TRY:
From the first try I identified three factors that I thought were preventing the formation of colors in the quench:
1. Water quality (I used distilled water this time.)
2. Aeration. (I areated the water this time.)
3. Shielding. (I made kind of a cap out of 14Ga steel.)
The results:
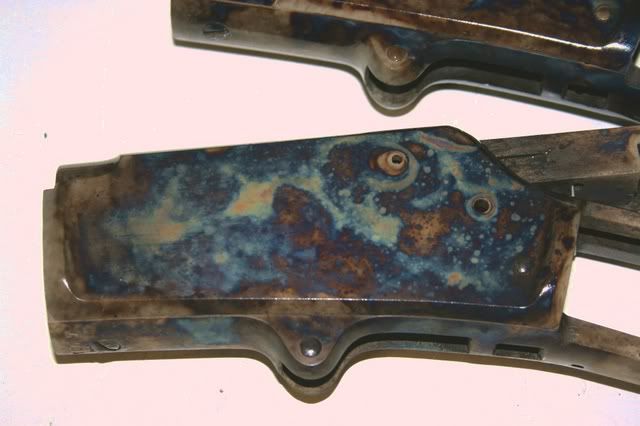
I changed my mix ratio from 2:1 to 3:1 wood to bone charcoal after looking at Don Anderson's 1893. (Thanks Don!). I would only classify this as very limited sucess- I got colors and they are close to "Marlin colors", but coverage and pattern is not consistent with Marlin colors. Some pieces like the buttplates had very little color.
Conclusion:
The parts were arranged in the crucible loosely, and the mix packed around them. Even though the pieces were in close proximity in the crucible, they were not tied together so that they would separate as the entered the quench. When I CCH single guns, I wire all the parts together so that they stay together as they enter the quench. I also use some shielding. All of this has the effect of creating more colors and patterns. I did not do this on this try since it appears from the film that Marlin packed their parts loosely.
I have come to the conclusion that if I follow what appear to be methods that Marlin used in the film, I will not get "Marlin colors". I suspect that if
I modify the methods that I will get very close. On the next try I will wire tie the parts together, just like I would do if I was doing a single gun. This will be the only difference in the next try.
They say that the third time is a charm!
-jim
Posted: Sat Feb 24, 2007 9:41 pm
by Jim D
Here's a little better photo:
I would normally apply lacquer or Truoil to the CCH'ing if I was going to keep it. In this case, I just sprayed some oil on it.
-jim
Posted: Sun Feb 25, 2007 9:26 am
by Hunt4em
Jim,
Nice colors! It's amazing how the slightest variation in the process will give drastic results. I noticed that you changed your ratio from 2:1 to 3:1 wood to bone. What would the out come be if it were reversed? (1:3) Do you make your own charcoal? I've read where they collected the buffalo bones off the plains to use as charcoal and bone meal. It may sound stupid, but with most of today's cattle going through feed lots and being injected with hormones, makes me wonder if that might be a slight variation. I will attempt this someday, but until then I'm looking forward to seeing more of your results. Thanks for the update.
Thanks, John
Posted: Sun Feb 25, 2007 10:52 am
by Jim D
John,
That's the most frustrating thing about learning how to CCH. There are a lot of factors that affect success, and if one of them is off, you either have
unacceptable results, or no results. Also, there is so much misinformation out there, that if followed, will ruin a gun very quickly. From my experience, the quench is the single most important factor governing the results. How do the parts enter the water? How far do they drop through the air? Are they shielded? Is the water aerated? How pure is the water? What temperature is the water? All these aspects of the quench will govern the outcome.
Bone charcoal acts as an energizer for the process. This is due to the fact that it contains Tricalcium Phosphate. I have done experiments using powdered Tricalcium phosphate in lieu of bone charcoal and obtained acceptable colors. So, it really doesn't matter whether it comes from cow bones, buffalo bones or pigeon dung, the results should be very close to each other. I haven't actually tried the pigeon dung! The amount of Tricalcium Phosphate in the mix does govern the colors that you get. The steel also governs the colors. If you CCH'd a Marlin, Winchester and a Colt, all in the same crucible, all quenched together, you would get diffferent colors because of the slight differences in the steels. I changed my mix ratio after looking at Don's 1893 because I knew from past experience that that mix would produce those colors if everything else was right. If I had made the mix a 3:1 bone to wood ratio, I would have a lot of pink, orange white and bright blue. About the highest wood to bone ratio I have used is 2:1 on Remington Rolling Blocks. I'll post a picture of some of these so you can see how the different ratios affect the colors.
I'm glad to hear that you're interested in trying this some day! The MOST
important thing to remember is don't believe what you read on the internet, or are told, or even the instructions that come with your CCH'ing kit about temperatures!!! You will hear that you should carburize and quench at anything from 1450F to 1750F. DON"T DO IT!
-jim
Posted: Sun Feb 25, 2007 11:15 am
by Jim D
John,
Here are a couple of photos of Remington #1 Sporting rifles that I CCH'd
with a 2:1 wood to bone charcoal ratio. Notice that there are more of the
"rainbow" colors with the higher percentage of bone charcoal.
-jim
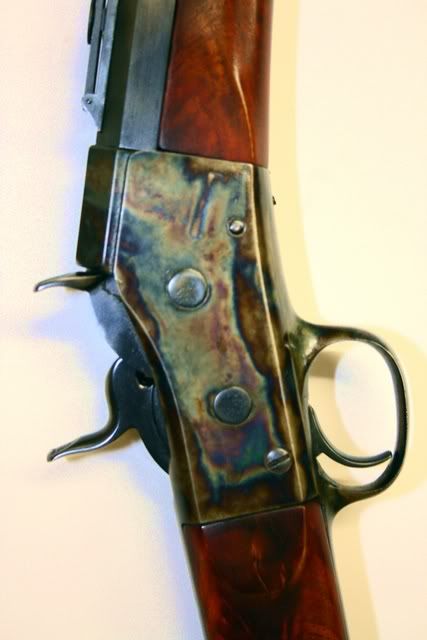
Posted: Sun Feb 25, 2007 3:40 pm
by Four-Eyed Buck
Very nice, Jim. Those little tweaks you did made a difference. In the current SHOOT magazine( Jan., Feb. issue), there's an article on Turnbull's work. IIRC, there's mention of salt in his quench. If you can find the issue( hard to do, wasn't available around here. Had to order direct from the publisher) , you might find some further info to help.......Buck
Posted: Sun Feb 25, 2007 3:44 pm
by Four-Eyed Buck
Jim, went back to your pics and looked again. The colors you attained are very similar to what's on my current manuf.'d CBC 1894( circa 2002). Not sure who cased the parts, might have been NEF as Marlin owns them now......Buck

Posted: Sun Feb 25, 2007 5:41 pm
by Jim D
Buck,
I tried salt in the quench about ten years ago. Salt in the water causes the parts to cool quicker, which makes them harder. Even though they cool quicker, it helps prevent warping and cracking. I've never figured that one out, but it's true. Anyway, salt is used in the quench a lot for industrial case hardening. I've heard that the way that you tell if the salt
content is high enough is that an egg will float in the water. I wonder why
Turnbull would be using salt? I'll have to see if I can get ahold of a copy of the magazine. Thanks for the tip!
-jim
Military Remington RB that was quenched in salt water. Notice the difference in paterns and colors from what you normally see if the part is quenced in water.
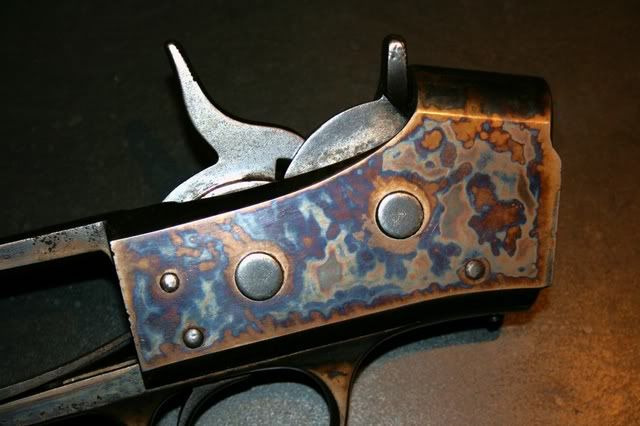